Epoxy floors are strong against impact, abrasion and even corrosion from harsh chemicals. They are also hygienic and repel salt that clings to tires on wintry roads.
Professional installation crews work swiftly and efficiently to create eye-catching, durable floors. They have proper licensing and insurance for client peace of mind. They also monitor temperature, humidity and substrate moisture to avoid curing and environmental defects.
1. Substrate Issues
One of the biggest factors in determining whether an epoxy floor will succeed or fail is the condition of the substrate. Even if you use the best possible resin and hardener, a weak substrate will eventually cause the coating to crack or delaminate from the concrete.
To ensure the strongest possible bond, the surface must be thoroughly cleaned and prepped. While a DIYer can get away with using a power scrubber and a bucket of water, professional contractors will typically use a diamond grinder or a shot blaster to prepare the floor for coating. A professional can also test the concrete to determine its strength level, which will dictate how much primer should be used.
Moisture issues can also be problematic for an epoxy floor. Blistering can occur if the substrate is too wet or if moisture migrates upward through the coating. These issues can be prevented by testing the substrate with a moisture meter and by using moisture mitigation products to prevent any potential problems from occurring.
Another issue that can result from a wet substrate is the formation of air bubbles in the coating. These bubbles can be difficult to break and may result in a marred or splotchy finish. These problems can be avoided by testing the substrate with a moisture vapor meter and by applying the coating during warm weather or by preconditioning the product.
Other common problems with a DIY epoxy floor include the presence of dust particles and oil or grease. These can interfere with the epoxy’s ability to adhere to the substrate and lead to an uneven or splotchy finish. It is important to sweep and vacuum the floor regularly to remove these particles. Additionally, it is crucial to keep the flooring clear of heavy vehicles or equipment until the epoxy is fully cured.
2. Poor Mixing
Epoxy floors are a durable and long-lasting flooring choice that adds both beauty and functionality to any room. They are hygienic, easy to clean and come in many different color choices and finish types. However, as with any construction project, mistakes can happen that can compromise the integrity of the finished product. These include improper surface preparation, mixing ratios, air bubbles, moisture and inadequate curing. These issues can lead to the failure of your epoxy floor and leave you with a costly mistake that will be difficult to correct.
A common error is not thoroughly mixing the resin and hardener before applying it to the floor. It is important to mix the two products with an electric mixer or drill to ensure a thorough, consistent mixture. Entrapped air can lead to an uneven appearance and prevent the epoxy from curing properly.
Another common mistake is not allowing the epoxy to cure thoroughly before using the floor. It is essential to allow the floor to fully cure before exposing it to heavy traffic and other chemicals. The time needed to cure the epoxy will vary depending on the product you use and the temperature in the room.
Professional epoxy installation services offer a more durable and longer-lasting floor than DIY kits. They take extra care to prepare the subfloor and carefully monitor the humidity levels during the application process. They also know how to correctly mix the resin and hardener to create a durable floor coating that will last for years.
It is also important to note that many epoxy manufacturers have detailed directions on how their products should be used. These directions are designed to help users avoid common problems and make the most of their investment in a quality epoxy floor.
For those considering epoxy flooring options, professional installation services can offer peace of mind and superior results compared to DIY kits. Additionally, reputable providers may offer the opportunity to view some epoxy flooring samples, allowing you to visualize the potential beauty and durability of your future floors before making a decision.
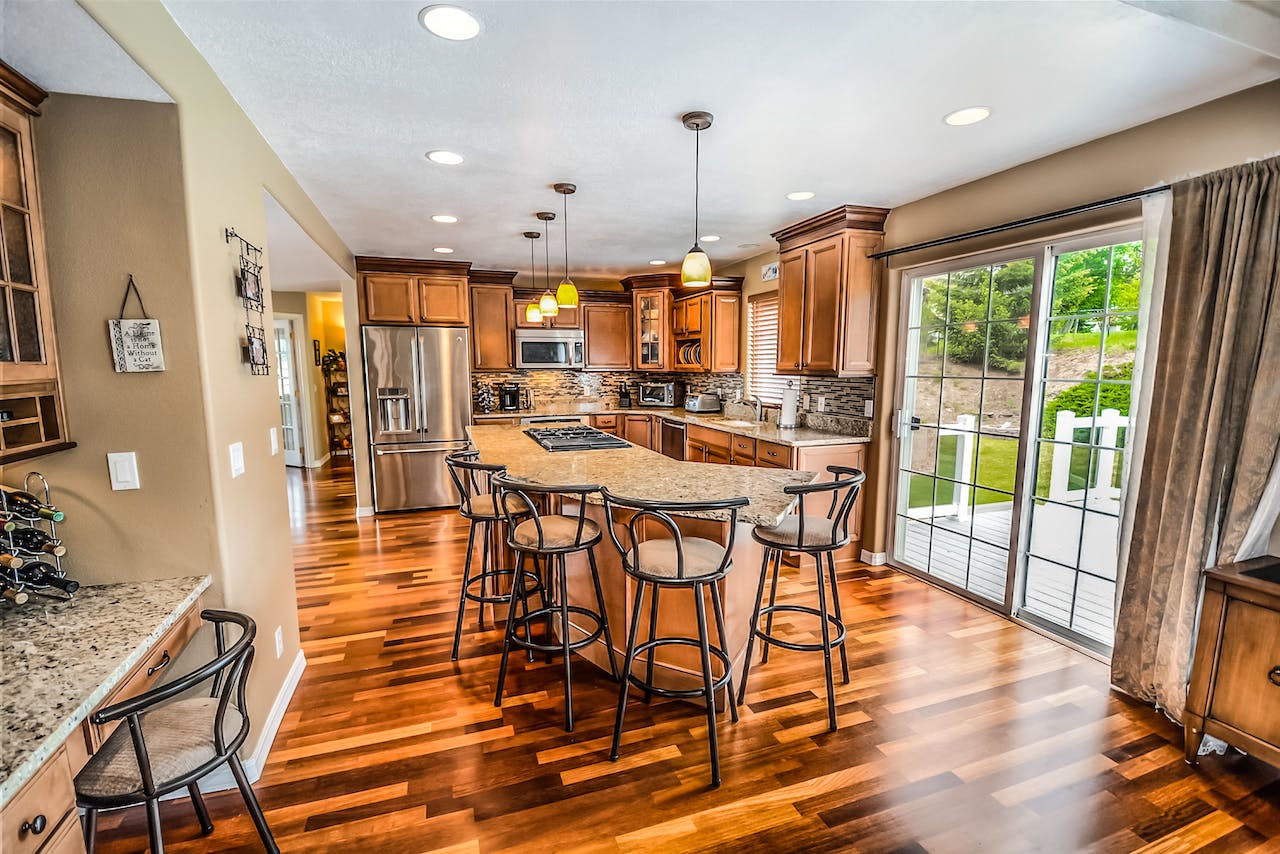
3. Environmental Issues
Epoxy floors are extremely durable and easy to maintain. They’re resistant to spills, grease, oils and most cleaning products. That’s why they’re often used in garages, auto shops and warehouses. However, epoxy floors may have a negative impact on the environment in some ways. For example, they are not eco-friendly when they contain harsh chemicals that can be harmful to people and animals.
Choosing an epoxy flooring material that is free of toxic chemicals is a great way to make a sustainable choice for your home or business. There are many different options for this, including using an epoxy floor coating that is natural and derived from sustainable resources.
An epoxy resin needs the right environmental conditions to set. If the humidity is too high or too low, it can affect how well the epoxy cures. This can lead to premature cracking and other problems.
Additionally, the temperature of the room should be stable to ensure that the epoxy sets correctly. Otherwise, it can become wavy or cloudy. This can affect the appearance of the floor, making it less attractive than it should be.
Whether you’re looking to revamp your existing floor or are in the process of building a new garage, an epoxy floor is a smart and stylish option. Just be sure to follow the manufacturer’s recommendations for when heavier shelving and vehicles can be reintroduced. It’s also important to check in on the floor regularly and clean it as needed. Doing so will help keep your floor looking beautiful for years to come!
4. Poor Adhesion
Professionals know the right prep work and application steps to take in order to ensure good adhesion between concrete and the epoxy. When DIYers do not do this correctly, they run the risk of a floor that looks less than professional and does not hold up to heavy use over time.
One of the main reasons that an epoxy floor starts to fail is because there is poor adhesion between the concrete and the resin coating. This happens because of contamination from improper prep or a number of different environmental factors.
Contaminants like fatty acids, silicone, siloxane, and acrylics can soak in deep enough to affect the adhesion of future applications even if the concrete was properly prepared. Other issues that can cause poor adhesion include the use of a solvent not recommended for your product, surface tension effects from the substrate, and wetting problems. Fish eyes are a visual anomaly that is caused by an incompatibility between the substrate and the coating. Moisture can also cause a number of problems, so it’s important to perform a moisture test using a calcium chloride-based kit ahead of time.
Another problem that may occur with poor adhesion is air bubbles. These tiny pinhead-sized bubbles appear sporadically or in honeycomb clusters and are caused by air entrapment in the mixture of Part A and Part B. This is commonly due to mixing at too high a speed or applying the resin too quickly, and it can result in a weaker epoxy coating.
Finally, sunlight and chemical exposure can discolor the epoxy and give it a yellow or unprofessional appearance. This can be due to a number of factors, including the wrong type or amount of hardener, and it can also happen if the floor is exposed to a lot of UV light for a long period of time after application.
5. Poor Curing
Many DIYers are eager to apply epoxy flooring as a cost-effective solution to their concrete floors. While epoxy is a durable and attractive floor covering, it can crack and delaminate over time, especially when the substrate underneath is weak or damaged. When this happens, the epoxy will pull away from the substrate, leaving behind a weak or damaged concrete surface and a mess for you to clean up.
To help ensure the quality of your finished floor, you should take steps to prepare the concrete surface and follow the instructions for applying the epoxy. The concrete surface should be free of grease, oil, dirt, and any other contaminants that may cause the epoxy to fail. To do this, a professional contractor will use a diamond grinder or shot blaster to remove the existing coating and create an optimal substrate for bonding. Most DIY epoxy coating kits will instruct the user to wash and acid etch the concrete floor, which is a good idea if the concrete has stains or other damage that can’t be removed with cleaning products.
You should also pay close attention to the proportions of epoxy resin and hardener, as this can affect the quality of your finished flooring. If you don’t have the right ratio, the epoxy floor will not cure properly, which can lead to blisters and other problems.
You should also keep in mind that weather conditions can influence the curing process. If the air temperature is too hot or too cold, it can alter the product’s viscosity and prevent it from setting properly. High humidity can also cause moisture to form under the epoxy, which can lead to different problems, including peeling.